Quality Management System Adalah
Guide To Data Quality Management Metrics Process And Best
What Is a Quality Management System (QMS)?
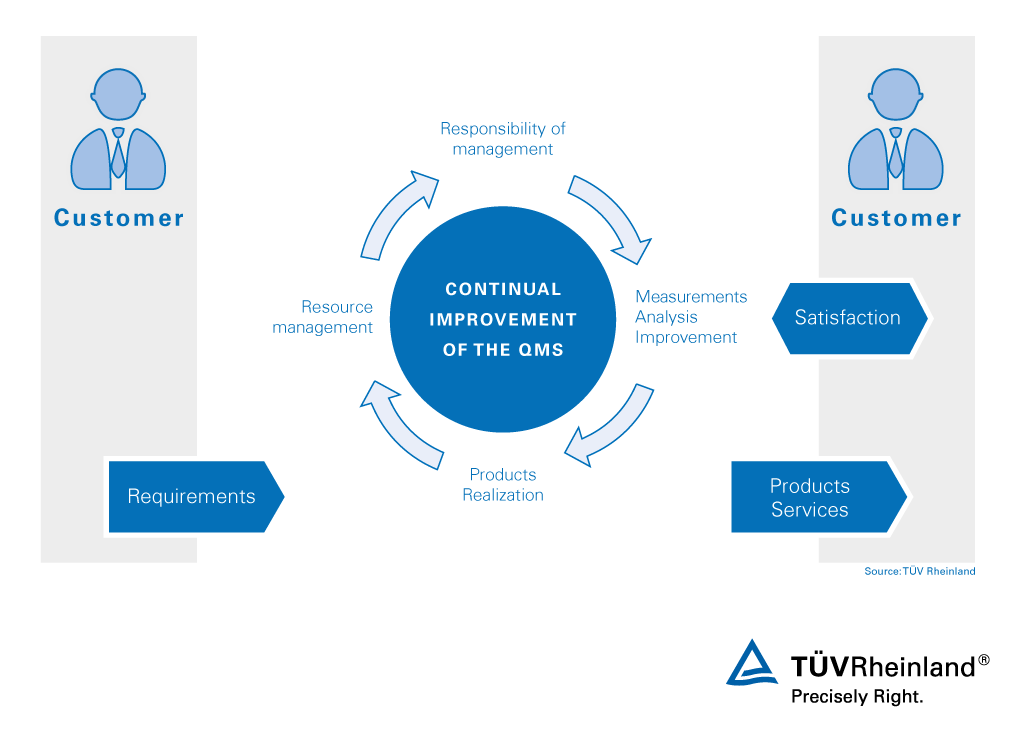
Quality Glossary Definition: Quality management system (QMS)
A quality management system (QMS) is defined as a formalized system that documents processes, procedures, and responsibilities for achieving quality policies and objectives. A QMS helps coordinate and direct an organization’s activities to meet customer and regulatory requirements and improve its effectiveness and efficiency on a continuous basis.
ISO 9001:2015, the international standard specifying requirements for quality management systems, is the most prominent approach to quality management systems.
While some use the term "QMS" to describe the ISO 9001 standard or the group of documents detailing the QMS, it actually refers to the entirety of the system. The documents only serve to describe the system.
Quality management systems serve many purposes, including:
- Improving processes
- Reducing waste
- Lowering costs
- Facilitating and identifying training opportunities
- Engaging staff
- Setting organization-wide direction
Implementing a quality management system affects every aspect of an organization's performance. Benefits of a documented quality management system include:
- Meeting the customer’s requirements, which helps to instill confidence in the organization, in turn leading to more customers, more sales, and more repeat business
- Meeting the organization's requirements, which ensures compliance with regulations and provision of products and services in the most cost- and resource-efficient manner, creating room for expansion, growth, and profit
These benefits offer additional advantages, such as helping to communicate a readiness to produce consistent results, preventing mistakes, reducing costs, ensuring that processes are defined and controlled, and continually improving the organization's offerings.
ISO 9001:2015 and other quality management standards
ISO 9001:2015 is the most recognized and implemented quality management system standard in the world. ISO 9001:2015 specifies the requirements for a QMS that organizations can use to develop their own programs.
Other standards related to quality management systems include the rest of the ISO 9000 series (including ISO 9000 and ISO 9004), the ISO 14000 series (environmental management systems), ISO 13485 (quality management systems for medical devices), ISO 19011 (auditing management systems), and ISO/TS 16949 (quality management systems for automotive-related products).
Elements and requirements of a quality management system
Each element of a quality management system helps achieve the overall goals of meeting the customers’ and organization’s requirements. Quality management systems should address an organization’s unique needs; however, the elements all systems have in common include:
- The organization’s quality policy and quality objectives
- Quality manual
- Procedures, instructions, and records
- Data management
- Internal processes
- Customer satisfaction from product quality
- Improvement opportunities
- Quality analysis
Quality Management System (QMS) Principles
Establishing and implementing a Quality Management System
Before establishing a quality management system, your organization must identify and manage various connected, multi-functional processes to help ensure customer satisfaction. The QMS design should be influenced by the organization’s varying objectives, needs, and products and services provided. This structure is based largely on the Plan-Do-Check-Act (PDCA) cycle and allows for continuous improvement to both the product and the QMS. The basic steps to implementing a quality management system are as follows:
- Design
- Build
- Deploy
- Control
- Measure
- Review
- Improve
Design and Build
The design and build portions serve to develop the structure of a QMS, its processes, and plans for implementation. Senior management should oversee this portion to ensure the needs of the organization and the needs of its customers are a driving force behind the systems development.
Deploy
Deployment is best served in a granular fashion by breaking each process down into subprocesses and educating staff on documentation, education, training tools, and metrics. Company intranets are increasingly being used to assist in the deployment of quality management systems.
Control and Measure
Control and measurement are two areas of establishing a QMS that are largely accomplished through routine, systematic audits of the quality management system. The specifics vary greatly from organization to organization depending on size, potential risk, and environmental impact.
Review and Improve
Review and improve detail how the results of an audit are handled. The goals are to determine the effectiveness and efficiency of each process toward its objectives, to communicate these findings to the employees, and to develop new best practices and processes based on the data collected during the audit.
industrial influence on quality and standardization
The history of quality can trace its roots back centuries when craftsmen began organizing into unions called guilds. When the Industrial Revolution came, early quality management systems were used as standards that controlled product and process outcomes. As more people had to work together to produce results and production quantities grew, best practices were needed to ensure quality results.
Eventually, best practices for controlling product and process outcomes were established and documented. These documented best practices turned into standard practices for quality management systems.
Quality became increasingly important during World War II, for example, when bullets made in one state had to work with rifles made in another. The armed forces initially inspected virtually every unit of product. To simplify the process without sacrificing safety, the military began to use quality techniques of sampling for inspection, aided by the publication of military-specification standards and training courses in Walter Shewhart’s statistical process control techniques.
The importance of quality only grew after the war. The Japanese enjoyed a quality revolution, improving their reputation for shoddy exports by fully embracing the input of American thinkers like Joseph M. Juran and W. Edwards Deming and shifting focus from inspection to improving all organization processes through the people who used them. By the 1970s, the U.S. industrial sectors, such as electronics and automobiles, had been broadsided by Japan’s high-quality competition.
The Rise of Quality Management Systems
The American response to the quality revolution in Japan gave birth to the concept of total quality management (TQM), a method for quality management that emphasized not only statistics but approaches that embraced the entire organization.
In the late 20th century, independent organizations began producing standards to assist in the creation and implementation of quality management systems. It is around this time that the phrase “Total Quality Management” began to fall out of favor. Because of the multitude of unique systems that can be applied, the term “Quality Management System” or “QMS” is preferred.
At the start of the 21st century, QMS had begun to merge with the ideas of sustainability and transparency, as these themes became increasingly important to consumer satisfaction. The ISO 19011 audit regime deals with both quality and sustainability and their integration into organizations.
Gallery Quality Management System Adalah
Project Quality Management According To The Pmbok
Configuration Management Wikipedia
What Are Quality Standards List Of Iso Quality Management
What Is A Ticketing System It Ticketing System Explained
214852 Quality Managament Quality Assurance Quality
Iso Management System Standards
Ncr Car Iso Quality Management Applications By Tacticom
Quality Management System Software Tools Pilgrim Qms
Project Quality Management According To The Pmbok
What Is An Effective Performance Management System Clear
Iata Security Management System Sems
Quality Management System Qms Bambang Priyambodo S Weblog
Sistem Manajemen Mutu Quality Management System Pekerjaan
Bs En Iso 9001 2015 Quality Management Systems Requirements
Iso 9001 Certification Wo Tuv Rheinland
Hotel Property Management Systems Pms Products And
0 Response to "Quality Management System Adalah"
Post a Comment